Technique Background
Generally, we often dispose waste plastics by burying in landfills, making PE granules as well as pyrolysis. Burying in landfills not only occupies the land, but also damage the environment. Making PE granules can extend the service life of waste plastics, however, after repeated used, the waste plastic is also hard to dispose eventually. Pyrolysis technology can convert waste plastic to fuel oil and carbon black by using high temperature heating, which is proved to be safe, energy-saving and high efficiency.
Prescription
The raw materials can be waste plastics, tyres, rubber, or the mixture of waste plastic and rubber, or swill oil, waste cooking oil, waste engine oil, pine, etc. Take 1000 raw materials and add 25-35 sodium carbonate, 20-30 magnesium carbonate, 30-40 potassium carbonate into the container according to mass ratio. Then heat the container by 350-420℃ high temperature for 7 hours, and then we get diesel fuel and exhaust gas. Cool down to 23-27℃, and the exhaust gas enters filtration tank. After filtration, the gas is discharged and the diesel fuel is stored in oil tank.
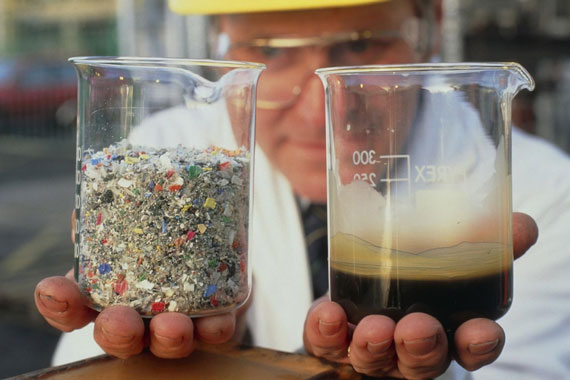
Case One
Take 1000 waste plastics and rubber into electric high pressure processing capsule, and add 30kg sodium carbonate, 25kg magnesium carbonate and 35kg potassium carbonate at the same time and then heat to 380℃ for 350min. After the chemical reaction, we get diesel fuel and exhaust gas, both of which enter cooling pond, and cool down to 25℃ (from gas to liquid). The exhaust gas containing toxic gases and dioxins enters filtration tank. The filtration tank has two cells, both of which contains lye. After filtration and activated carbon adsorption filter layer, the exhaust gas meet environment requirement, and we get 820kg diesel fuel stored in the oil tank. The waste dregs in the electric high pressure processing capsule can generate carbon black. The waste plastic materials can be film, disposable syringes, medical plastic bottles.
Case Two
Take 1000 mixture of waste plastic and rubber into container. The plastic and rubber can be arbitrary mass ratio. Add 28kg sodium carbonate, 23kg magnesium carbonate and 33kg potassium carbonate into container at the same time. Heat the container by 395℃ for 7h and then we can get diesel fuel and exhaust gas. Cool down to 26℃, and the exhaust gas enters filtration tank. After filtration, the exhaust gas can meet environment requirement. We get 680kg diesel fuel in the oil tank.
Characteristics
The pyrolysis technology has the characteristics of simple production process, easy operation and low cost. The diesel fuel output rate can reach as high as 82% and the diesel fuel is in line with national standards. It also takes full use of waste, turns waste into wealth, realizes resources recycling and meets the national environmental protection requirement.