1. Introduction
With the development of automobile industry, the demand for tires and other rubber products is also increasing. At the same time, waste tire production also has increased dramatically. The accumulation of a large number of waste tires not only occupies the land, pollutes the environment and harms the health of residents, but also is very easy to cause fire. Resulting in a huge waste of resources, and it is more and more dangerous “black pollution”. Therefore, the treatment of waste tires has become a very urgent environmental and social problem. At present, the disposal of waste tires can be roughly divided into four kinds, namely, accumulation or landfill, incineration, bio-degradable. Four methods have their own advantages and disadvantages. From the perspective of environmental protection and resource conservation, recycling is the most ideal method, which includes refurbished tires, reclaimed rubber, preparation of rubber powder, pyrolysis and other processing methods. The pyrolysis of waste tires is one of the most potential recycling methods.

The pyrolysis of tyres is an incomplete thermal degradation process conducted in the anoxic or inert gases, which can produce liquid, gaseous hydrocarbons and carbon residue. These products after further processed can be transformed into high-value products for a variety of purposes, for example, the carbon residue is converted into carbon or activated carbon, while the liquid product is transformed into high-value fuel oil and chemical products such as olefin and benzene, and gaseous hydrocarbons is directly used as fuel. Obviously, the waste tire pyrolysis treatment can achieve the maximum recycling and reuse of resources, and has high economic and environmental benefit. So it represents the development direction of today’s waste tire disposing.
2. Components of waste tires
Tires are mainly made of rubber (natural rubber and synthetic rubber), carbon black and a variety of organic, inorganic additives (including increasing plasticizer, antioxidant, sulfur and zinc oxide). In general, the number of components contained in the tire tread compound is 55%~6o% rubber, 30%~6% carbon black, 33% ~ 9% organic additive, 3%~6% inorganic auxiliary agent. Tire rubber is mainly generated by natural rubber (NR) and synthetic rubber (SR) through the sulfur occurring crosslinking reaction. Synthetic rubber usually is styrene butadiene rubber (SBR) and butadiene rubber (BR).
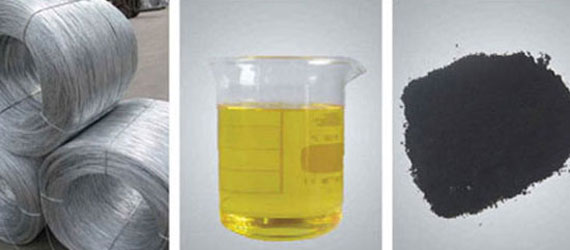
3. Overview of tyre pyrolysis process
Waste steel wire is separated after the tires are cleaned, cut, crushed and magnetic sorted. The remaining materials through drying and preheating are fed into pyrolysis reactor. Under the protection of inert gas, such as steam or nitrogen, the reactor begins to pyrolyse. According to the different target materials, the processes are also different. There are processes for preparing fuel oil, carbon black and combustible gas.
Firstly, the process for preparing fuel oil:
If the target material is fuel oil, the process can make the generated gaseous hydrocarbon and carbon residue as the fuel for the pyrolysis reactor, in order to realize the pyrolysis of the waste rubber blocks. And the pressure relief method is used to separate the oil and gas rapidly.
Secondly, the process for preparing carbon black:
The oil and carbon black can be considered as products, which should be solved from the carbon residue to carbon black, that is, after the removal of waste steel slag from the solid recovery materials by magnetic separation, and then through the fine grinding, pickling, filtration, drying processes, we finally get carbon black products.
Thirdly, the process for preparing combustible gas:
The process of combustible gas production is scarce. Because the gas production accounts for the total production only 4%~11%, carbon residue accounts for 37%~40%, and oil accounts for 55%. The pyrolysis gas is condensed and further processed to obtain the synthesis gas. The general waste tire pyrolysis process is shown in the following figure.
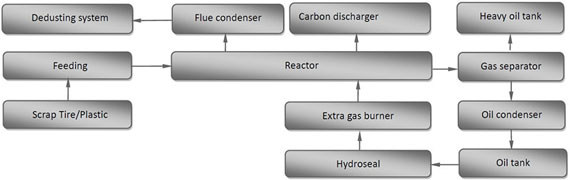