Introduction of continuous pyrolysis process
The pretreated plastic, tyre, rubber, sludge or medical waste are conveyed to the horizontal pyrolysis reactor through auto feeding system. Then there will be oil gas generating gradually when the temperature rises up to 500℃. The oil gas will be cooled down and transformed into liquefied oil by spray cooling system. The liquefied oil goes into the oil tank; at the same time, a part of gas that can’t be condensed goes into hot air circulation heating system by secondary fire retardant damper, and it will be recycled for heating reactor as gas material. Exhaust gas goes to the strong spray dedusting system for removing pollutant, and then the gas can be discharged to the air. The pyrolysis slag emissions and is recycled through second sealed discharging system.
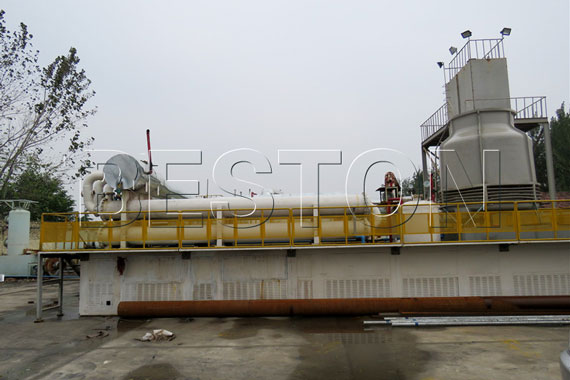
Main component systems of Beston continuous pyrolysis plant
1. Stable and no rotary pyrolysis reactor;
2. Pre-treatment devices: tyre shredder machine and plastic dryer machine, medical waste disinfection system (if necessary);
3. Automatic feeding system;
4. Hot air circulation heating system;
5. Spray cooling system;
6. Secondary fire retardant damper;
7. Strong spray dedusting system;
8. Oil gas recycling system;
9. Automatic discharging system;
10. Pressure and temperature multipoint monitoring system;
11. Central electric control system
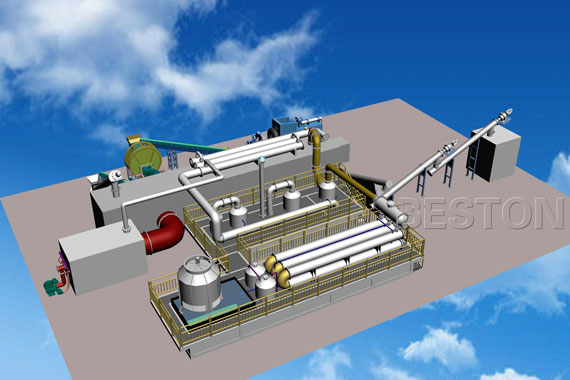
Comparison in technology between traditional solid waste treatment plant and continuous pyrolysis equipment
1. The traditional pyrolysis plant with high energy consumption; energy can’t be fully recycled; the poor tightness of equipment; the goal of energy saving and environmental protection can’t be fully realized during the production process; high energy input increases production costs; the intermittent feeding and discharging system is low efficiency and takes higher labor cost.
2. The latest continuous waste plastic pyrolysis plant adopts the screw feeding sealing system technology, which is hold by the company’s invention patents, hot air heating furnace circulating heating technology, heat drying technology with high heat exchange efficiency and capacity. Impeccable electrical control system saves labor costs. Three waste utilization reasonable recovery can basically realize of zero emissions, safety and environmental protection.
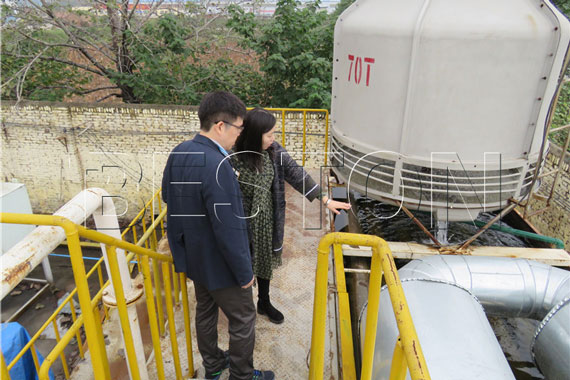
Comparison between the way of traditional plant and that of pyrolysis process
1. The latest continuous waste pyrolysis plant produces some gas, which is enough to meet the needs of device self-heating and reduces additional fuel consumption. The plant can use its own end products as a recycled energy heating for the whole recycling process.
2. Compared with the burning furnace, the new device has simpler operation, less operator to a large extent, so that it can save the operating costs.
3. The pyrolysis oil can be directly used as the fuel oil for heating, and it can be further classified and processed, then formed oil products such as petrol, diesel with high benefits.
4. The pyrolysis ash can be used as ingredients for building materials.
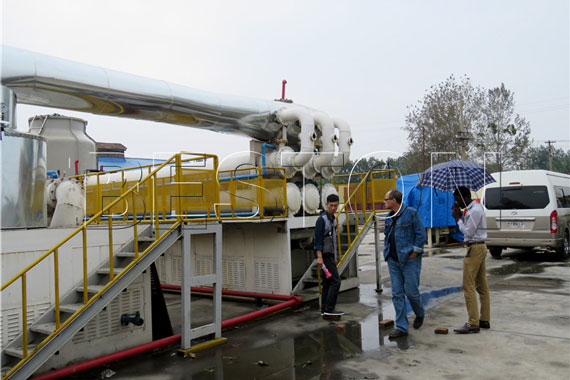
The pyrolysis product rate of all kinds of waste tire, rubber, plastic materials
material | Item | fuel oil | steel wire | carbon black | combustible gas |
tires | truck tires | 45%-50% | 15%-20% | 30% | 5%-10% |
car tires | 40-45% | 10%-15% | 40% | 5%-10% | |
motorbike bike tires | 30%-35% | 5%-10% | 10% | 5%-10% | |
rubber | cable | 25%-35% | |||
shoe sole | 25%-35% | ||||
mixed shoe sole | 20%-30% | ||||
slipper | 20%-30% | ||||
waste fiber carpet | 30% | ||||
PMMA | 40% | ||||
other mixed rubber | 35% | ||||
waste plastic | PE | 85%-95% | |||
PP | 80%-90% | ||||
PS | 80%-90% | ||||
ABS | 40% | ||||
pure white plastic | 60%-70% | ||||
fishing net, safety net | 45%-50% | ||||
MAMEI | 40% | ||||
plastic brand | 20% | ||||
pulp | 20%-30% | ||||
daily life rubbish | 30%-50% | ||||
pure plastic cable | 60%-80% | ||||
pure purchase bag | 50% |